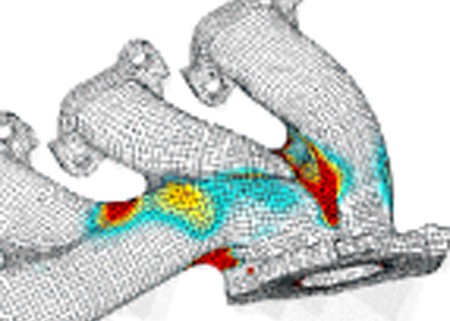
Industries including Automotive, Aerospace and Power Generation sectors
Components such as exhaust manifolds, cylinder heads, turbo-charger housings and turbine blades
Full capability for all relevant aspects of material testing
Solutions for more robust constitutive modeling of many materials under TMF loading conditions
Simulation tools for reliable durability analysis and life-time prediction
Thermo-Mechanical Fatigue (TMF) analysis is a truly material-centric problem. Typically TMF occurs in high-value power-producing applications, either by component cost (turbines) or by volume (automotive powertrain). Design of such a component requires a robust treatment of the time and history dependant behavior of the materials over a broad range of temperatures, and hence the use of advanced constitutive equations in the structural FEA modeling. Some examples of NWN Z-mat solutions follow:
Grey Iron
NWN Z-mat has material models for cyclic TMF loading of grey or grey cast iron (GI/GCI), which have tension/compression asymmetry. In order to provide reliable fatigue life results, the NWN Z-mat models can be combined with a Z-post durability analysis using the Smith-Watson-Topper model based on the viscoplastic strain range.
SiMo Irons
These materials exhibit a wide range of properties over a typical TMF loading cycle: a rise in durability above room temperature, then a sensitivity to tensile yielding at intermediate temperatures, followed by a continued increase in ductility above 700C reaching large strains to failure. The unified viscoplastic framework of NWN Z-mat accounts for these changing parameters, and the extended Sehitoglu life-time prediction model considers plastic strain range to provide accurate results.
Cast Aluminum
For these materials, NWN Z-mat model that includes time/temperature dependent viscosity and hardening modulus, two or three back stress terms, and aging effects can capture the behavior fairly accurately. Viscocity effects causing higher plastic strains can partially offset life reduction at high temperatures, but ensuing creep damage in tension is an important factor. Either the extended Neu-Sehitoglu or the Chaboche TMF model can be used to predict fatigue life time for these materials.
Stainless Steels
Stainless steels are oxidation-resistant, and can hold stress at elevated temperatures (unlike SiMo irons which see stress relaxation at high temperatures). The stress applied at elevated temperature turns out to be a damaging mechanism, and low-cycle fatigue strength and low strain rate ductility decrease at elevated temperatures. These materials are well analyzed with the NWN Z-mat gen_evp unified viscoplastic model, and a fatigue model that accounts for the cyclic plastic strain range and maximum temperature.
Superalloys
Superalloys are typically used at elevated temperatures due to their stress-carrying capacity, and are subject to aging effects due to the high percentage of alloying elements and their precipitates. The life time prediction of the NWN Z-mat gen_evp model that includes aging effects, combined with the Chaboche stress based fatigue life model, shows good correlation with experiments.